prefab UNIBUILD
Only one precast mould shape required to manufacture all building components.
01-04 STRUCTURAL COMPONENT RANGE
Prefab UNIBUILD
The UNIBUILD PREFAB TECHNOLOGY was recently nominated for the 2024 SMART BUILDING INDUSTRY AWARDS
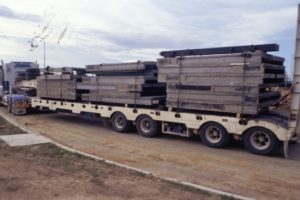
90% of the above precast panel load is weightless thermal insulation. 10% of the load is Unibuild steel fibre concrete applied in thin layers surrounding the insulation rendering the panels structural, fireproof and floodproof.
Loading can be maximised for the loaders full capacity. (Four loaders would be required to transport the equivalent house volume of a “factory transportable” building, requiring escort vehicles and police resource time. and limited travel times.
Prefab UNIBUILD components are less than 2400 mm wide so can travel 24/7 on any road in the country. Short offload time and early structural completion on site in a couple of days is a major plus.
SYDNEY BUILD EXPO 2018
Our Sydney Build 2018 exhibition was seen by over 4000 visitors. The Unibuild Technology received two nomination for The Australian Construction Industry Awards in the categories of “Product Innovation” and “Offsite Construction of the Year”.
View Unibuild’s Display Left wall.
View Unibuild’s Display Rear wall.
View Unibuild’s Display Right wall.
UNIBUILD IS SEEKING A MASTER LICENSEE FOR WORLD WIDE TECHNOLOGY TRANSFER. CONTACT ME, PETER SMITH, FOUNDER AND DIRECTOR, at peter@unibuild.com for further details.
Technical Details of more than 300 Unibuild Off-Site Modular Buildings Now Available For Technology Transfer
To view all PLANS go to Unibuild Projects – PRECAST
The UNIBUILD Bush-Fire Proof Building Technology.
Back in 1952, when I was a school boy in Canberra, Australia, a raging bush-fire swept in from the south west burning all in its path. The fire burned over Red Hill and was eventually stopped at the fence lines of the residential and foreign embassy homes lining Mugga Way.
Our gang won the Radio Station 2CA bush fire donations appeal competition, thanks to a 5 pound check from the Dutch Embassy, which unfortunately lost its rear fence.
In 2003, again, a raging bush-fire swept in from the south west. However thousands of houses and other buildings had been built in suburbs south west of Red Hill in the path of the fire front. 500 buildings burned to the ground and 4 deaths recorded.
The bush needs fire for regeneration and fire paths repeat over previous paths. (Has been going on for thousands of years).
Early ACT building regulations insisted on a layer of tar paper be installed under the floor boards, in the wall cavities and under the roof tiles to limit condensation. (Tar paper consists of a thin layer of bitumen between two layers of brown paper). I physically fixed this tar paper during my days as a carpenter.
According to CSIRO fire research, when the temperature reaches 47.7 degrees C, the oil in eucalyptus leaves turns to flammable gas, and bitumen turns to flammable gas. So when fire surrounded the above houses the tar paper immediately burned causing the structures to explode. If you study TV footage of the Canberra 2003 fire you will see blue flames licking out from the gaps between the roof tiles. These are the flames of hydrocarbons, not burning leaves and small tree branches which burn red and yellow.
The only building material which remained in tact were the concrete paths, steps and posts.
Lately I have been researching the thousands of fire photographs of the recent, and current, bush fire damage to houses and buildings. I visited some of the sites when the King’s Highway reopened for access to the NSW south coast.
Most of the burned structures I investigated were older buildings and would have been lined with tar paper, a building regulation at the time of construction.
I think you can apply the same reasoning to all the other bush fire damaged regions.
Tar paper was later banned from construction regulations yet there are still thousands of older houses and other buildings containing this material still standing.
LESSON LEARNED. DON’T BUILD HOUSES USING FLAMMABLE OR NON FIRE-PROOF BUILDING MATERIALS.
In the mid nineties I was licensing The Unibuild Technology into the USA and based in San Diego, California. (Many gum trees grow in California).
One morning I visited a local shopping centre and noticed a small grass fire burning in an open field opposite. That evening the fire spread up a hill and burned down over 500 houses.
The developer of this sub division had a covenant on the house designs. All roofs were to be of Californian redwood shingles. A shingle in northern California has a moisture content above 95%. In southern California the moisture content reduces to about 3%. Thus all the roofs were reduced to firewood kindling.
The only building materials which remained in tact were the concrete paths, steps, posts and the ornamental masonry and concrete fireplace constructions. Concrete does not burn.
LESSON LEARNED. DON’T BUILD HOUSES USING FLAMMABLE OR NON FIRE-PROOF BUILDING MATERIALS.
Back in the 1970’s Unibuild began research into steel fibre reinforced concrete and gradually began using this material in its housing and other building projects, eliminating most traditional flammable building products and associated fixing trades.
Today, all Unibuild structural components for floors, walls, roof and other items are made from steel fibre reinforced concrete, either in solid form or encasing insulation slabs inserted to comply with building R value regulations. Thus the whole building structure is fire proof with a minimum fire rating of two hours, and six hours for the in-built columns and beams.
Bush-fires sweep through in a matter of minutes, and as concrete does not burn the fires cannot find any material in Unibuild structures to ignite and flame. (As a spin off, there is no need to pay exorbitant fire insurance premiums which rise and rise after every national disaster).
PHOTO. The Unibuild fire-proof display house, Canberra.
PHOTO. Internal photos and commentary. (UB5710-Photo2)
PLAN. Plans of fire and energy ratings. (UB5710-Plan)
THE UNIBUILD CLIENT DESIGN SHEET 1 (Client Design Sheet 01)
THE UNIBUILD CLIENT DESIGN SHEET 2 (Client Design Sheet 02)
The Difference between Unibuild “Off Site” Modular and Conventional Construction
The first Unibuild off-site modular home was built in Canberra in 1968. In 1969 we relocated to Perth, Western Australia, and designed and constructed many Unibuild modular masonry buildings requiring the labour of bricklayers. In the early 70’s Western Australia was booming and bricklayers were in short supply. They would quote a job, lay a couple of hundred blocks then demand a review of rates upwards.
Unibuild decided to eliminate the masonry trade in favour of its modular, insulated precast concrete walling components. In a public demonstration we commenced construction of two projects of identical design on the same day. One was the usual Unibuild modular masonry construction, the second was Unibuild’s first precast off-site modular construction. The following photographs show the advantages of Unibuild off-site prefabrication.
1410_050 Unibuild’s first truck load of insulated wall panels leaving for the site.
1410_034 Construction progress of the off-site modular house after seven days.
1410_067 Construction progress of the conventional masonry house after seven days.
UNIBUILD HAS NOT DESIGNED AND BUILT A CONVENTIONAL HOUSE SINCE.
Modular Construction:
- Takes only a few weeks to complete the entire project on site, depending on size.
- In the planning stage, off-site components are fully detailed to fit the specific needs of the customer’ project. (Each trade his its own detailed plan).
- Off-site factory space is used to manufactures all the structural components
- The only site work carried out are footing pads, sewerage and drainage works completed before the structural components arrive at the site.
- A crane erects the prefabricated components in 1-2 days. Add doors and windows and lock up after 4-5 days. The job is now weather proof.
- The interior trades, electrician, plumber and painter can all work together to complete the project.
- Nil or only minimum scaffolding is required
- Landscaping, driveways and paving can follow but are not critical trades.
Conventional Construction:
- Construction takes about 6-12 months or longer.
- At the planning stage, architects and engineers draw up one overall plan to be sorted out by all the trades. Usually no detailed co-ordination planning.
- All trades must follow in trade sequence. Drainage lines, ground slab, masonry construction, roof structure, roof tiling, etc. Cost of detailed supervision is high due to chasing up the various trade workers for scheduling.
- Wet weather can delay the project by months.
- The building need to be scaffold out around the perimiter, a very costly exercise.
- More internal trades required, eg. framers and plasterers needing to work in sequence.
- Landscaping, driveways and paving common to both methods of construction.
Unibuild’s Fire, Flood, Cyclone and other Hazard Proof “Off Site” Modular Building Technology
Read Peter Smith’s address to the Modular and Offsite Building Conference, Perth, on Unibuild’s fire, flood, cyclone and other hazard proof “off site” modular building technology.
Transcript (Unibuild_Conference_Script),
Photographs, (Unibuild_photographic Slides)
Remote Area Mobile Unibuild Precasting Plant.
Unibuild established a modular off-site precast plant in Far North Queensland, for the training of local Indigenous community unemployed workers wanting to design and build their own hazard proof housing and other buildings without having to rely on expensive and confusing “Consultant” documentation unsuited to FNQ climatic and indigenous living conditions.
RECENT REMOTE AREA PROJECTS.
9288 –Rain Forest Cabin (9288-plan)
9290 – Holiday Park Cabin (9290-plan)
9291 – Cabin and Caravan Storage Unit (9291-plan)
9300 – Granny Flat Shell (9300-plan)
9304 – FNQ Aboriginal Housing (9304-plan) (9304-3d-1) (9304-3d-2)
9306 – Factory Site Office (9306-plan) (9306-3d-1) (9306-3d-2)
9310 – Backpacker Accommodation (9310-plan)
9312 – Hospital Clinic, Aurukun (9312pl01) (9312-3d-1) (9312-3d-2)
9314 – Accommodation, Aurukun (9314plan) (9314-3d-01) (9314-3d-02)
9316 – 4 Bedroom House, (9316-plan)
9318 – 4 Bedroom House (9318plan1) (9318plan2) (9318-3d-1) (9318-3d-2)
9320- 2 Bedroom House (9320PL01) (9320plan2) (9320-3d-1) (9320-3d-2)
9322 – 3 Bedroom House (9322plan1) (9322plan2) (9322-3d-1) (9322-3d-2)
Unibuild – Proven Sustainability
Unibuild’s first modular, semi prefabricated, passive solar energy project was built in Canberra, ACT, in 1968. After 48 years of occupancy this house was recently sold for an exceptionally high price. It is good for another 48 years, and longer.
Flood Proof Building Technology
If all the houses and low rises buildings damaged and destroyed during the recent Australian floods had been built using The Unibuild flood proof technology they would have remained undamaged and habitable.
Fire Proof Building Technology
The loss of human life and property caused by the recent fires in Australia is regretable. Had the properties been built using The Unibuild Technology most likely all structures would have remained habitable.
To those wishing to rebuild, or build for the first time to prevent fire loss in a future similar event, we offer our fireproof building technology for consideration.
Unibuild fireproof structures comprise the floors, walls and roofs, all components having a minimum 2 hour fire rating to withstand the hottest bush fire as it sweeps through.
Please refer to photos then contact Unibuild for further information.
Download latest brochure. Page1, Page2, Page3, Page4.
5726plan Shows a plan of a small rural bushfire proof cabin.
Australian Institute of Building (NSW Chapter) Professional Excellence Awards
The Unibuild Technology wins the Presidents Citation for Research. (Photo)
Low Cost Housing, Chennai, India
Multi Level affordable housing structures. 40-50% lighter than traditional construction, fast building, high thermal insulation built-in, low maintenance. (Photo 9250).
Don’t Waste Your Money Re-inventing The Wheel
License the proven UNIBUILD modular prefabricated design and construct technology. Over 350 projects, applicable to any country, now available on DVD for easy technology transfer. Download latest schedule. PDF.
Unibuild Thailand
Commenced operations with the successful display of a model low cost modular house at the Bangkok BITEC exhibition. and a full size Unibuild shell house at Bangkok Architect 05. (arch05). National Housing Authority approved for low rise and high rise low cost housing projects. Withdrew following the GFC.
See Unibuild Jobs 9090A, 9090B, 9090C.
Tsunami and Cyclone Damage reconstruction
Unibuild Thailand is well placed to assist with the reconstruction process. Reconstruction technology has been completed for Thailand, Sri Lanka, Maldives, India, Bangladesh and Burma. (Tsunami A).
Unibuild Thailand, drawing upon Unibuild’s extensive earthquake and cyclone resistant modular building R & D in Australia and California, has developed low cost tsunami and cyclone resistant structural shells, for immediate occupancy, and later 2 story extension.